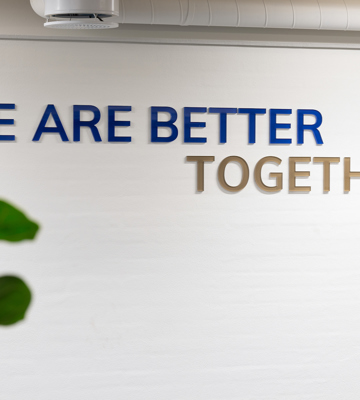
13-06-2025Career
Lots of new colleagues have joined Svanehøj
Svanehøj faced a major challenge in the spring, when travel restrictions, quarantine procedures and social distancing measures made it difficult for customers to travel to Denmark to have their pumps tested, as they usually do.
The solution was a digital setup, where customers are able to follow the procedure via cameras and Microsoft Teams for the 4-6 hours that a pump test typically lasts.
This applies to both performance tests in the production hall and to the more advanced string tests in Svanehøj’s test tower, with 1:1 simulation of the conditions out on the ship.
“We can chat, share screens and upload photos and videos via Teams. Customers can ask questions along the way and they can get involved as much or as little as they want. We can also record the entire session for later use. It’s incredibly easy and extremely flexible,” says Lars Foged, project manager at Svanehøj.
Lars Foged and Svanehøj have had many customers watching tests via screens since the spring. Lately, they have carried out a handful of tests for a large offshore customer, who has placed an order for 33 Svanehøj pumps for a project to convert a tanker into an FPSO unit.
For Lars Foged, Svanehøj’s remote testing concept is an excellent example that something positive can come from companies being forced to think in new ways during a crisis.
“COVID-19 is a huge challenge, but it’s also an opportunity to challenge habitual thinking. In the past, we spent a lot of resources on logistics and practical matters, as we needed customers to attend onsite pump tests. A digital setup requires fewer resources while offering substantial savings for the customer, who can avoid time-consuming travel and significant transport, food and accommodation costs,” he says.